Jindal Air Connect
Jindal Air Connect specializes in solutions for compressed air and fluids distribution and provides superior performing compressed air & gas systems with engineered longevity to reduce operating costs and improve productivity.
Compressed Air is required in manufacturing and industrial activities for a multitude of applications. It is used to control and regulate appliances and is the driving force for pneumatic drills, conveyors, spray guns, machine tools etc. For these appliances to function. correctly it is very important to ensure that the quality of air employed is excellent. In Air Connect pipes the inner surface of the pipe which comes in direct contact with air is made of polyethylene which unlike metal pipes guarantees absence of rust and impurities formed by condensation that could become detached from the pipe walls. Clean Air also means that the filters require less maintenance. Also Air Connect pipes are suitable for use at high operating pressures of upto 232 psi. Air Connect Pipes are bendable without springing back and come in coils of upto 200 meters which significantly reduces the number of joints in the piping system and improves air flow.
Air Connect, the NEXT-Generation pipe system is manufactured with the latest german technology at our state of the art facility in Dehradun, Uttarakhand, India. The performance is more reliable and designed for tropical conduction with very good sealing ensuring Zero leakage.
Air Connect is an innovative piping system for compressed air and inert gas distribution that uniquely combines all the benefits of plastic and metal in one pipe. Pipes and fittings are joined together using compression technique which has various benefits such as Fast and easy installation, no need to weld, glue, fuse or thread. Air Connect not only extends the life of the system, but significantly reduces leakage that leads to saving of time, labour and operating costs.
Air-Connect Alumnium Composite Pipe
Air Connect Pipes are constructed of an inner and outer layer of Polyethylene sandwiched over an aluminum core. All the layers are permanently bonded together by an intermediate layer of polyethylene based adhesive. The aluminum core is sealed by Over-lap welding technology which enables the pipes to withstand high working pressures.
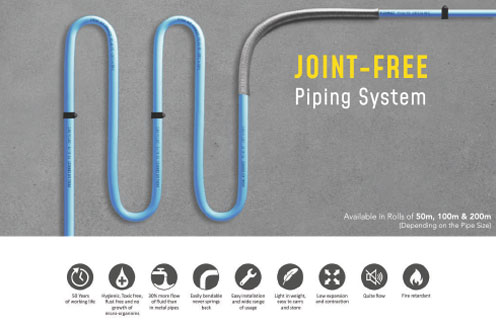
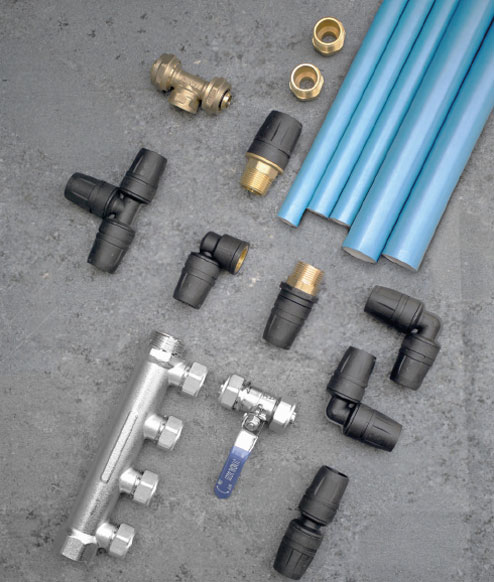
Piping System Design
1. Locate each process, work station, or piece of equipment that uses compressed air. They should be located on a plan, and a complete list should be made to simplify record keeping. This initial process will act as a beginning for your piping layout.
2. Determine the volume of air and pressure range required at each location. Information regarding pressure and flow rates of the equipment such as tools can be obtained from the manufacturer. If the pressure and flow rates are not known, assign some preliminary rates until the specific values can be obtained.
3. Determine the system conditioning requirements for each piece of equipment. This includes the allowable moisture content, particulate size, and oil content. The system may require conditioning equipment including dryers, filters, lubricators and pressure regulators.
4. Establish how much time the individual tool or process will be in actual use for a one-minute period of time. This is referred to as the 'duty cycle'. In most industrial applications, tools or operations of a similar nature are usually grouped together.
5. Establish the maximum number of locations that may be used simultaneously on each main, and for the project as a whole. This is known as the 'use factor'.
6. Establish the extent of allowable leakage. Leakage is a result of the number and type of connections, the use of disconnects, the age of the system and the quality of the initial assembly process. Many small tools and operations will result in more leakage then fewer larger applications. A well maintained compressed air system will have an allowable leakage rate of 2-59a.
7. Establish any allowance for future expansion. Thought should be given to over sizing some components (i.e., main supply lines) to avoid the cost of replacement at a later date.
8. Select the air compressor layout and assign a preliminary pressure drop for the system.
9. Select the air compressor type, conditioning equipment, equipment location, and air inlet, making sure that scfm (L/min) is used consistently for both the system and compressor capacity rating.
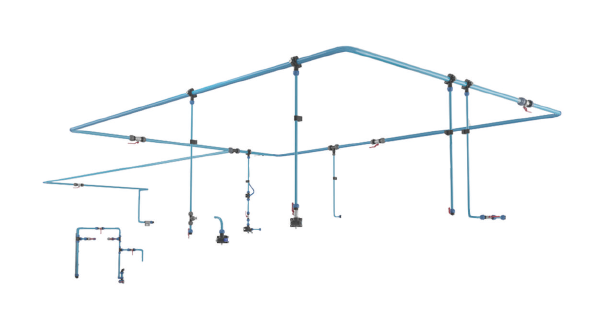
Jindal EZ-Fit Compression Fittings
E-Z Fittings combine the positive feature of high reliability with a simple installation technique that does not require any special tools. The permanent pipe joint is achieved by compression i.e. tightening the nut against the tapered split ring. The profiles of the two pieces are designed to cause a progressive shrinkage of the split ring and to distribute the compression forces across the contact surface. A seal housing has been designed with a special slip-proof profile called O-Rings that come into direct contact with the pipe.
EZ Fittings are made from high quality engineering plastic using advance injection moulding that makes it extremely reliable and reluctant to leakages. The fittings are rigid and lightweight at the same time.
The simplicity and economic aspect of this system is based on the use of spanners, standardised threads, which make it possible to connect with any system.
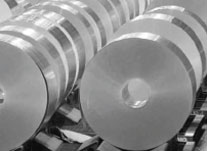
Raw Material - ALUMINIUM
Aluminum is a soH, lightweight, non-toxic and malleable metal with appearance ranging from silvery to dull gray depending on surface roughness. Aluminum alloys have yield strengths ranging from 200 mpa to 600 mpa.
For Air Connect pipes, a specialized grade of Aluminum is used which is manufactured specifically for these pipes and have the right balance of strength and flexibility as required for compressed air application.
Determining Pressure Loss In Jindal MLC Pipe
1. In order to use pressure drop charts, it is necessary to find the equivalent length of run from the compressor to the farthest point in the step. In addition to the actual measured pipe length, the eHect of fittings must be considered. This is because fittings create an obstruction to the flow of air. This degree of obstruction has been converted to an equivalent length of pipe in order to make calculations easy.
2. Determine the actual pressure drop that will occur only in the piping system. Since the air compressor has not been selected yet, this figure is variable. A smaller pipe size may lead to higher compressor horsepower. It is considered good practice to oversize distribution mains to allow for future growth and the addition of condition equipment that may add a pressure drop not anticipated at the time of original design. It should be noted that this practice may result in a higher initial cost for the piping system.
3. Size the piping using the appropriate charts, having first calculated the flow rate at the operating pressure and operating temperature, scfm, and the allowable friction loss in each section of the piping being sized. Since all pipe sizing charts are calculated using loss of pressure per some length of piping (100 ft (30.5m)), it is necessary to arrive at the required value for the chart you are using.
FEATURE COMPARISION | |||
---|---|---|---|
FEATURE | AIR CONNECT | ALUMINIUM PIPES | PPR-C PIPES |
COST | Most cost-effective. Low initial investment, long Working life and no maintenance. | Most expensive | Least Expensive but has a short Working Life |
HYGIENE | Hygienic, made from 1009¢ Food Grade Polyethylene | Hygienic | Not hygienic, is not made from Food grade material. |
FLOW RATE | Best, has smooth inner surface and minimum use of fittings. | Good, has smooth inner surface but use of more fittings (elbows and couplers) | Good, has smooth inner surface but use of more fittings (elbows and couplers) |
CORROSION RESISTANCE | Good | Good | Good |
BENDABILITY | Bendable without any spring back | Not bendable | Not bendable |
REQUIREMENT OF FITTINGS | Minimum, use of Elbows and Couplers is eliminated | High, fittings are required at bends and joints at every ó mts | High, fittings are required at bends and joints at every ó mts |
JOINING METHOD | Compression method, Leak proof, fittings can be re-opened for maintenance work | Push-in method | Electric fusion method, results in a permanent joint and cannot be re-opened for maintenance work. |
WEIG HT | Light-weight, Upto 90'¥• lighter than GI pipes | Heavy, 5 times heavier than Air Connect Pipes | Heavy, compared to Air Connect Pipes |
STORAGE, HANDLING & TRANSPORTAIION | Easy, are light weight and packed in coils of upto 200 mts. Come in Carton packing. | Difficult, are heavy and packed in lengths of 6 mts | Difficult, are heavy and packed in lengths of ó mts |
INSTALLATION | Fast and Easy. Requires basic Tools onIy | Fast and Easy. Requires basic Tools onIy | Time consuming, requires electricity and Heating machin e |
LINEAR THERMAL EXPANSION | Low | Low | Low |
WASTAGES | Zero wastage | High | High |
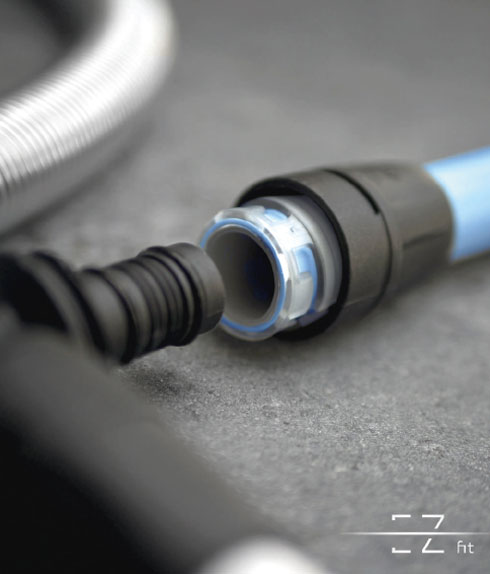
Take a look at our products by clicking the button below